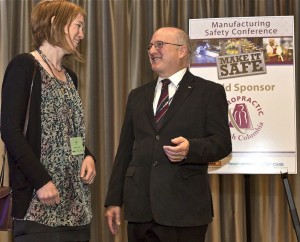
Yours truly Susan Main meets keynote speaker Terry Bogyo. Photo by Khalid Hawe
I met Terry Bogyo at the Make It Safe Conference recently after his keynote address “Rewire Your Safety Culture: Is there an app for that?”
Terry (whose last name is pronounced Bō-show) is WorkSafeBC’s Director of Corporate Planning and Development – and, as I expected, his answer was no – there is no app that can re-wire your safety culture.
Certainly there are many great apps that support safe practices, but none of them has what it takes to create that level of change.
“That re-wiring has to be in you, regarding the way you think about safety,” he told delegates from the manufacturing and food processing industries. “Just because you have an app, it doesn’t mean you’re going to change things. To change things, you have to use them appropriately.”
Terry talked about the importance of having senior management support for changing safety culture – a topic I covered recently in my post Senior management support for safety, in which I shared advice from Donna Wilson, WorkSafeBC’s VP of Industry Services and Sustainability.
“It can’t just be ‘Thou shalt be safe,'” Terry told delegates. “Having conversations about safety is not the same as buying new equipment.”
Lean Six Sigma
Terry described this managerial approach to improving processes – in this case, workplace safety. He talked about using Lean Six Sigma – a combination of Toyota’s Lean Manufacturing and the Six Sigma approach created by Motorola.
A company using the Lean Six Sigma approach ensures its people, processes, and focus are centred around a shared goal to improve safety processes and eliminate wasteful actions.
“The difference between the two trends is that Six Sigma tools focus on improving the quality of a product or service, whereas Lean focuses on eliminating waste and improving cycle time in a production process,” wrote Michael George in his 2002 book: Lean Six Sigma. “Integrating Lean Production methods with the quality tools used in Six Sigma produces faster and greater performance improvements, resulting in increased growth and profitability.”
I was especially curious to meet Terry – after reading his blog Workers Compensation Perspectives – and writing about his thoughts on what the manufacturing industry needs in my post Changing safety culture in manufacturing.
“Every worksite has a safety culture,” Terry said. “It may be good or bad but it is real and it is an important determinant in work-related injury and disease. I’ve seen examples in Canada, US, and Australia where individual firms have set out to change their safety culture and succeeded.”
Thanks to FIOSA-MIOSA, WorkSafeBC, and the Canadian Manufacturers and Exporters of BC for a great conference. I’ll have more stories to share about other safety folks I met – so stay tuned.
Pingback: Only you can re-wire your safety culture « Musculoskeletal Injury Prevention & Lift Training
This is a great article about safety in the work place. As a company in the construction and architecture industry, it is especially important for us to ensure safety among our workers. Thankfully our product, StoneLite®, is so lightweight that it does not require heavy machinery to install. This advantage helps us avoid possibly hazardous situations for our workers.